Grinding polishing sand-blasting
Grinding Polishing Sand-blasting
Adapt the characteristics of your parts to your needs!
Cylindrical grinding
Grinding is still often the only way to get your mechanical part dimensions and geometry “to within a few microns”.
We have several machines that can adapt to all your parts: providing grinding of both large and smaller parts, either one-off or in series, of varying shapes, …
Our special grinding discs will cut the hardest part base materials or coatings.
In particular, after the eventual electroless nickel plating of your products, we can rework it to accurately adjust it to your needs.
We can provide grinding services: maximum diameter 350 mm, maximum length between centres 1000 mm
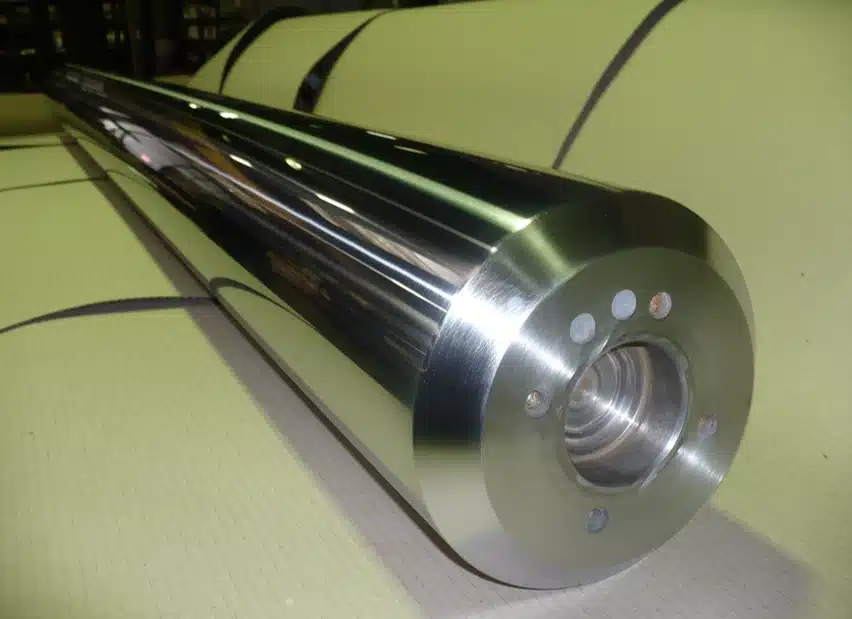
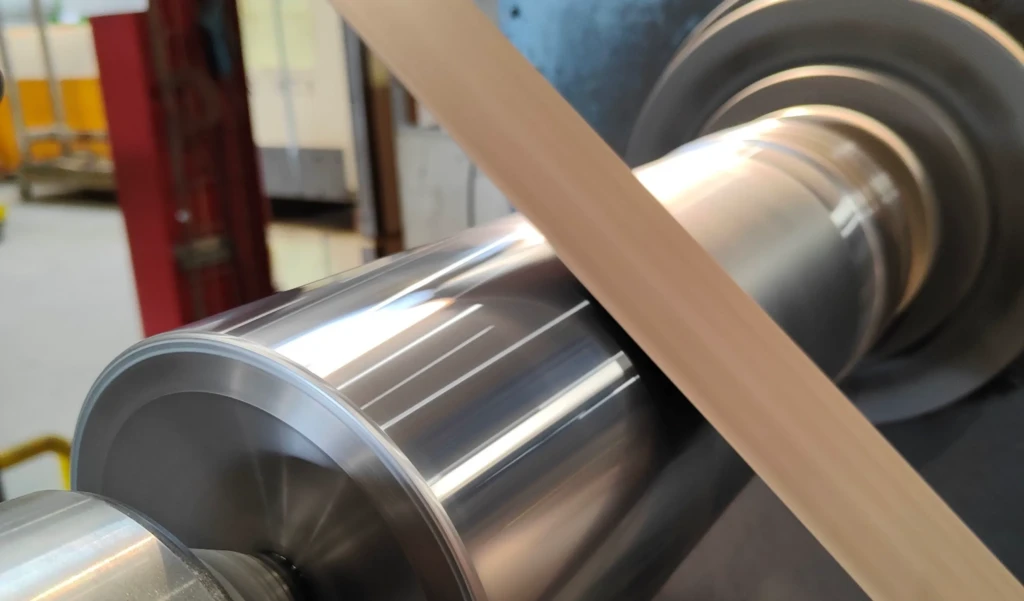
Industrial polishing
Polishing and bead-blasting
Industrial sandblasting is an industrial cleaning and stripping technique. An abrasive is projected at high speed using compressed air through a nozzle onto the material to be stripped.
It is also used to modulate the surface finish of parts before or after nickel plating depending on your needs (up to 10µ Ra).
Projecting sand at high speed onto a surface has several effects:
- it strips;
- it deoxidises;
- it removes a fragile surface layer.
In such cases, industrial sandblasting is then used as pre-treatment preparation.
But it can also be used to give the part the roughness required for its final use.
When the abrasive is round, such as glass beads, a satin finish is obtained. Bead blasting is used to finish welds.
Small and medium-sized parts can be processed in a sand-blasting cabinet. This stripping solution allows you to work comfortably by containing the abrasive and bead-blasting dust inside the machine.
Our cabinet is equipped with a continuous abrasive recycling and cleaning system. Large parts are processed directly on a lathe, with the part rotating and the spray nozzle advancing automatically.